Fast
Strong
Accurate
No reverse marking
Leak proof
Tamper proof
Single side access
Portable equipment
Reduced handling
No weakening of parent material
Can be automated
These benefits of stud welding are best understood by examining the problems it solves when replacing the following processes:
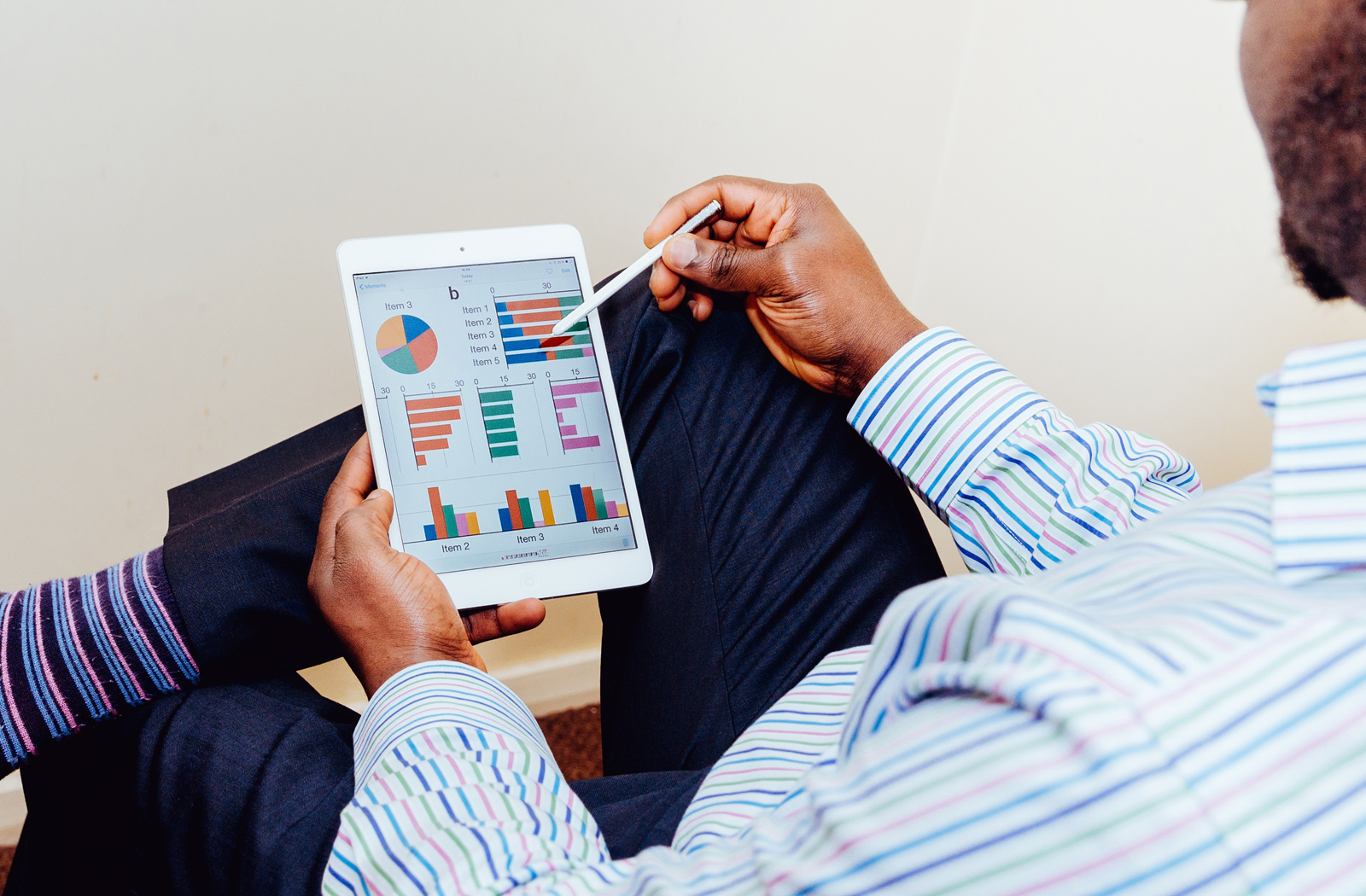
Pressed inserts:
This method of fastening can work loose, crack point and leave stains. Holes have to be punched and debunked, these holes weaken the parent material. On the reverse side the insert is visible and unsightly and the joint is not guaranteed leak-proof. Finally there is a handling problem in having to take the workpiece to a fixed machine
Drilling and tapping:
These are very slow processes and in order to achieve full joint strength the parent material has to be thicker. If a through drilled hole is used then it has to be sealed or the use of a blind hole requires cleaning out. Drills and taps break and there is a possibility of the fastener working loose.
Back welding:
This is a slow messy and inaccurate process. Holes need to be drilled or punched and the fastener held in place. Time has to be spent finishing the reverse side to grind off excess material and burn marks.
Through Bolting:
This is both cumbersome and slow in that it requires two handed assembly with access form both sides. Holes weaken the parent material, there can be leakage stains from the unsightly bolt heads and it is not tamper-proof.
Projection & Resistance Welding:
Time is wasted in taking to a fixed machine. Costs are increased owing to high power consumption and having to replace electrodes.
Soldering & Brazing:
The prolonged heat required in this slow process causes distortion. Furthermore it is difficult to hold fixings accurately in place.
Riveting:
Once again holes are required, rivets look untidy and they can work loose. They can not be undone so this process is not reversible.
In Summary:
Studwelding is a fast, accurate and reliable process which ensures that the joint is stronger than the parent material or stud. Product design is improved by eliminating reverse marking, there is no heat distortion and the area around the weld is clean and flat. Access is required from one side only and because the equipment is mobile component handling is reduced. The results are a tamper proof, leak proof fixing which can be used on materials where the reverse side is pre-coated, painted or polished. The workpiece is not weakened by a hole so thinner material can be used. Corrosion problems can be eliminated and there is no need to clean and finish. The portable equipment is easy to use and if high production rates are required the process can be automated.
Leave a Reply